Ayr Cane Farm
Energy Savings: 5% | Cost Savings: $939 | Capital Cost: $26,160 | CO2 Savings: 2.5 | Project Status: implemented
Industry:
Sugarcane
Location:
Dry Tropics
Pump Type:
Centrifugal, Turbine
Irrigation Type:
Flood
Technology:
Irrigation and Pumps
The farm is 118 ha and irrigated all-year-round producing around 143 units per ha per year. Energy consumption varies with seasons, being highest in summer.
The annual energy consumption for the site during the 2018-2019 period was 65,500 kWh at a cost of $18,500, and energy consumption on the farm consists mainly of:
- Irrigation system: 11kW centrifugal pump, 15kW centrifugal pump with VSD, and a 15kW line shaft turbine pump (bore pump).
A recent energy audit showed how improving the current systems can lead to energy and cost savings. The audit recommendations are:
- Tariff Change: Change from transitional tariff 66 that will be phased out during 2021 to optimal tariffs 33 and 20 in two NMIs.
- Motor upgrade for the 11kW centrifugal pump: with a higher efficiency model to better match the VSD, improving the power factor of the system.
- Replace the bore pump and wet end: to potentially improve the capacity of groundwater extraction from 23 ML to 360 ML per year, improving pumping flexibility and the system’s ability to meet crop water requirements. Reduced surface water charges have been estimated at $11,600 per year, not included in the cost savings.
The auditor also recommended analysing the implementation of a solar PV system once the irrigation system is updated.
Table 1. Costs and savings from audit recommendations.
Recommendation | Annual Energy Savings (kWh) | Annual Costs Savings ($) | Emission Savings
(tCO2-e) | Capital Cost ($) | Payback Period (Years) |
Tariff Change | – | 3,111 | – | – | – |
Motor upgrade | 941 | 282 | 0.8 | 3,800 | 13 |
Replace bore pump and wet end (considering 23ML pumped) | 2,287 | 680 | 1.8 | 22,360 | 32.6 |
Total | 3,228 | 4,073 | 2.6 | 26,160 | 22.8 |
The grower proceeded with the replacement of the bore pump and the upgrades of the centrifugal pump motor. The savings made have been measured in a Measurement and Verification (M&V) process, as outlined in Table 2.
Table 2. Estimated and Actual energy and cost savings.
Metric | Audit estimation | M&V calculation | Variation (%) | |||
Motor | Pump | Motor | Pump | Motor | Pump | |
Energy Savings (kWh) | 941 | 2,287 | 1,488 | 1,645 | 58 | -28 |
Cost Savings ($) | 282 | 680 | 446 | 493 |
The greater savings obtained from the M&V calculations compared to those estimated in the audit for the motor pump upgrade, have probably been influenced by the higher capacity of the model installed, with the farmer electing to install a motor with a 180 L frame instead of a 160L frame.
In the case of the pump replacement, the lower savings are probably due to the pump not operating at the best efficiency point, operating at a lower end of its tolerance or due to a different water level in the bore.
From the implementation of recommendations in the audit, the farm has reduced energy consumption and costs by 5% of the total energy used on-farm, with Carbon emission savings of 2.5 t/CO2-e per year.
Table 3. Pre and post implementation energy and costs improvements.
Metric | Pre-implementation | Post-implementation | Reduction (%) |
Energy Consumption (kWh) | 65,500 | 62,367 | 5 |
Cost ($) | 18,500 | 17,561 | 5 |
An energy audit is a good investment
An energy audit is a great first step in moving a business towards a more efficient future by reducing energy use, costs and carbon emissions on site.
The Energy Savers Plus Extension Program was delivered by the Queensland Farmers Federation with support and funding from the Queensland Department of Energy and Public Works.
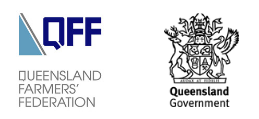